What are Lighter-Than-Air Systems
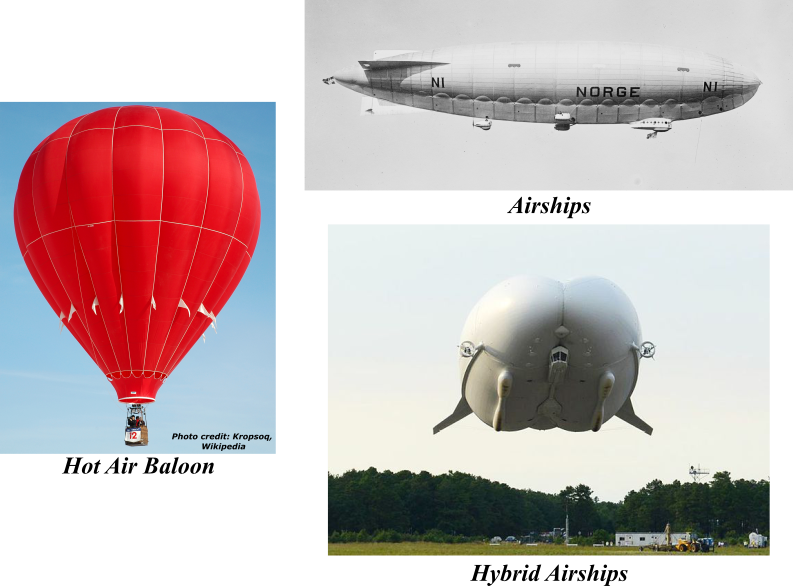
Lighter-than-air systems are the flight systems deriving a significant amount of their lift from the buoyancy effects related to lighter than air gases like hydrogen, helium and methane. Contrary to fixed-wing aircrafts LTA systems are associated with minuscule fuel consumption with their mobility expanding across extremely harsh terrains. LTA systems are further segregated into three different categories, viz. hot air balloons, aerostats and airships. Hot air balloons derive their lift completely from the buoyancy effect, whereas the later two make use an additional aerodynamic lift component to remain airborne. Due to the mitigated dependence of LTA systems on powered propulsion to generate the required lift, fuel consumption related to these systems is significantly lower compared to heavier-tha-air aircrafts. Moreover, owing to their unique VTOL (Vertical Takeoff and Landing) feature, LTA systems do not require a very sophisticated ground handling infrastructure. However, the biggest disadvantage related to these flight systems is thet LTA systems require a calm weather condition to carry out a smooth flight. Notwithstanding this shortcoming, the increased demand for green aviation technologies and increased fuel expenditure, LTA systems are witnessing a steep resurgence across the scientific, academic, commercial and defence sectors globally.
Airships
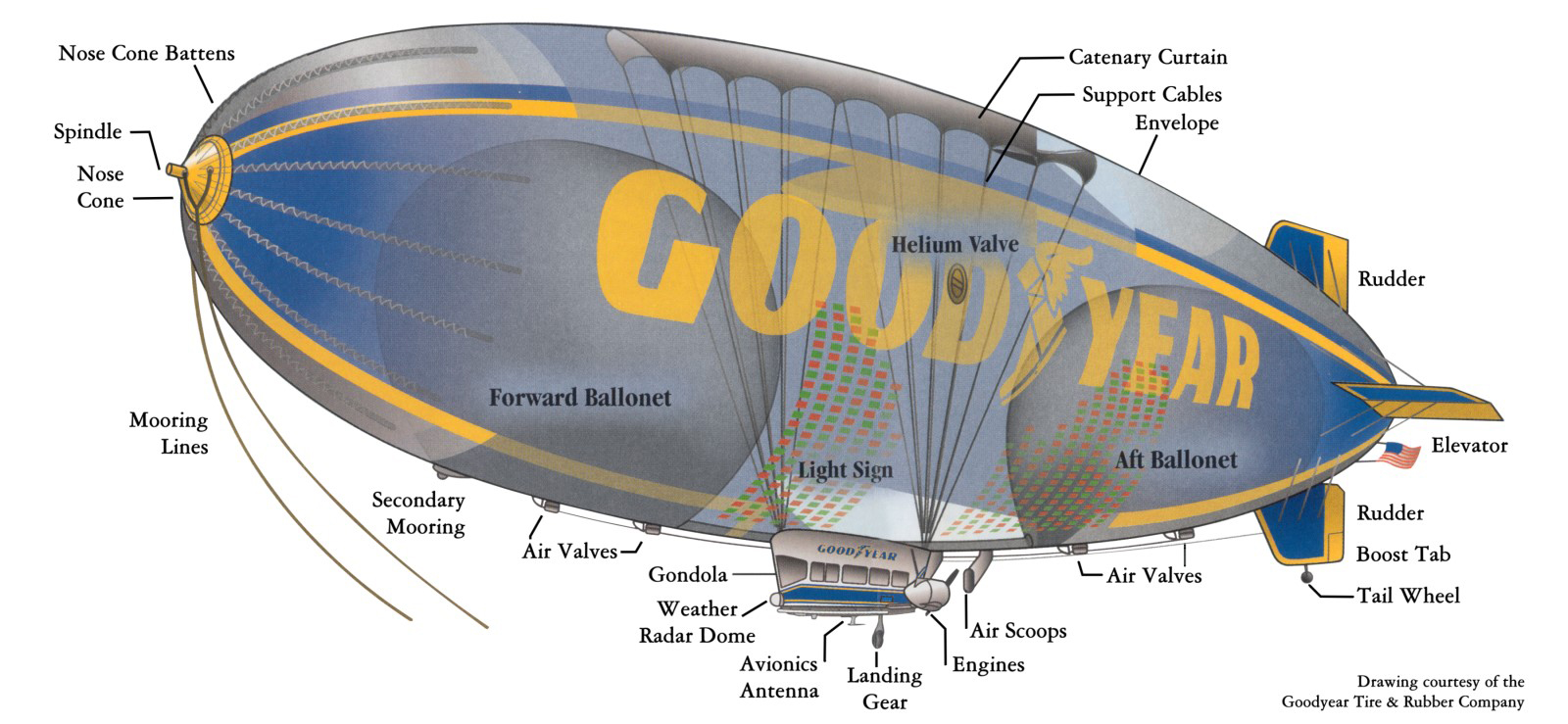
The airships operate by the Principle of Archimedes: "Bodies submerged into a fluid receive from it a lifting force which is equal to the weight of the displaced fluid." The airship is filled with a lifting gas (Helium). The atmospheric air has a higher specific weight than the lifting gas. The airship envelope filled with the light gas generates a lift that is equal to the weight of the displaced air and the airship floats in the heavier air. As the pressure inside the envelope is very low, (about 5.0 millibar or 1/15 psi), a hole in the envelope results only in a very slow leak, taking hours or even days to affect the airship's performance. As the airship rises, the helium expands and helium contracts when the airship descends. This might lead to the change in shape of the hull. In order to maintain the shape, a ballonet is installed (or in some airships: multiple ballonets) inside the hull of the airship. These are simply bags containing air, which are inflated or deflated to maintain a constant pressure inside the envelope. This allows the helium to expand and contract. When the ballonet is completely empty the airship is said to be at its "pressure height." The initial design of the ballonet size will determine an individual airship's maximum altitude capability. In addition to the lift provided by helium, analogous to a conventional aircraft, modern airships derive aerodynamic lift from the shape of the envelope as it moves through the air. Maximum payload capacity may be achieved by making a running takeoff in an airship, much like an airplane. The speed gained on the ground is converted to lift when the pilot raises the airship nose. Once airborne, airships can perform numerous activites like aerial surveillance, cargo transportation, mobile communication etx. while remaining nearly geo-stationary for extended periods of time.
Aerostats
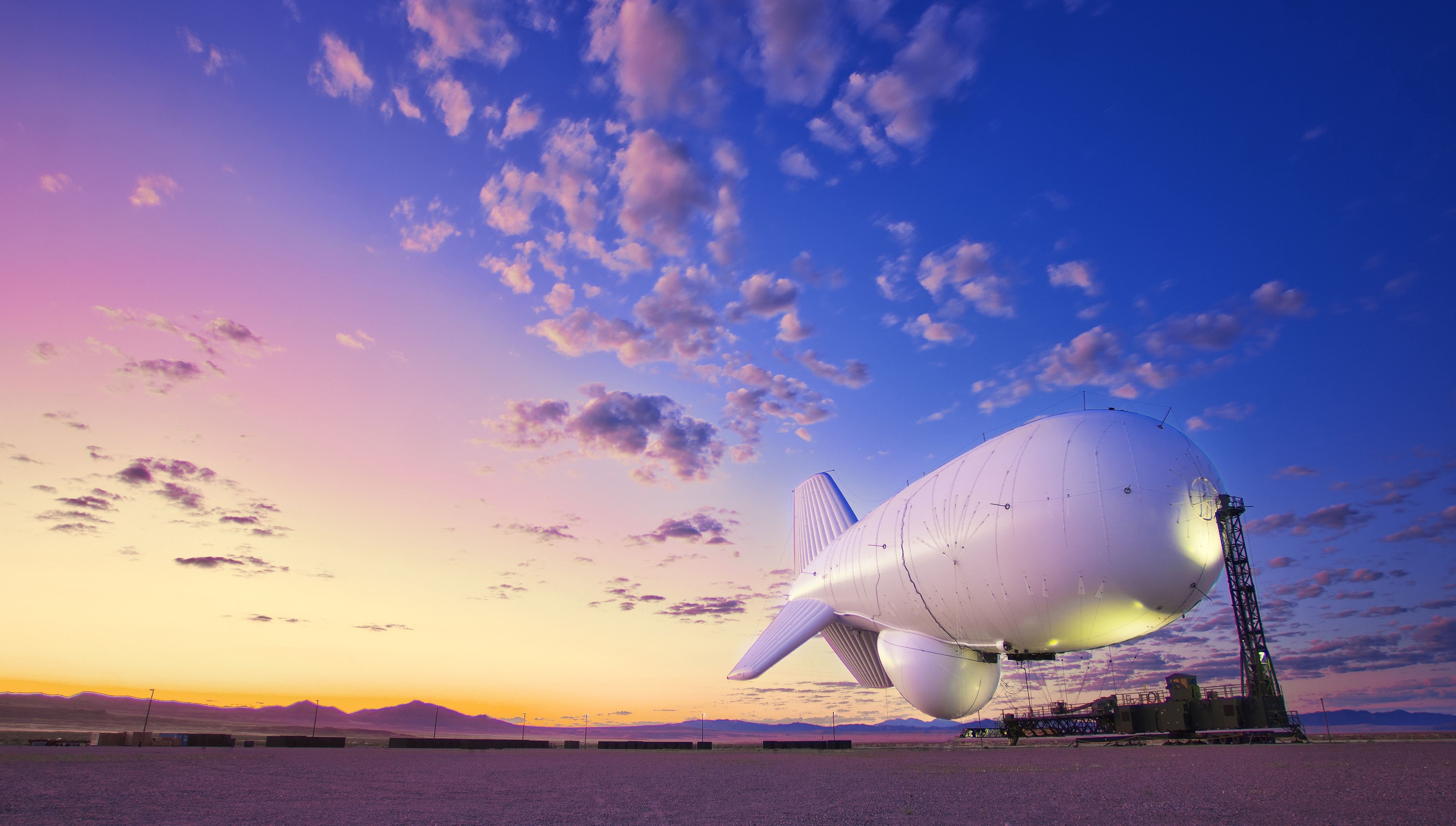
About aerostat.