Screws
Contents
Introduction
Well we all know what screws are, but nevertheless we’ll provide you with the bookish definition.
A short, slender, sharp-pointed metal pin with a raised helical thread running around it and a slotted head, used to join things together. [1]
As can be seen in the image below, the cylindrical portion of the screw from the underside of the head to the tip is known as the shank. The shank may be fully threaded or partially threaded. Pitch is the distance between each thread. [2]
The majority of screws have a right handed thread, meaning that they are tightened by clockwise rotation. A very good mnemonic device for remembering this when working with screws or bolts is righty-tighty, lefty-loosey. [3]
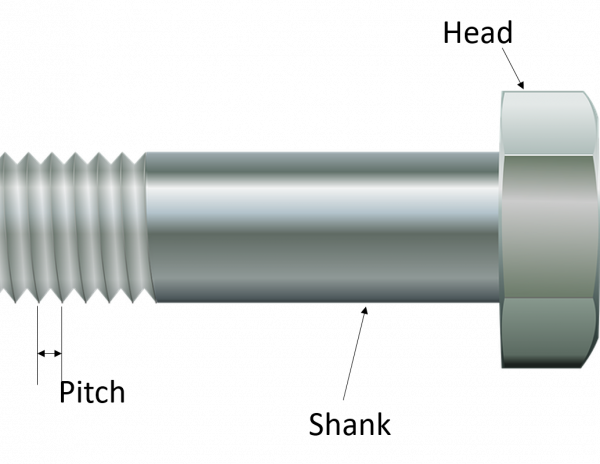
Screws v/s Bolts
Both screws and bolts are externally threaded fasteners.
A bolt is designed for insertion through holes in assembled parts. It is normally intended to be tightened or released by torquing a nut.
A screw is capable of being inserted into holes in assembled parts, of mating with a preformed internal thread or forming its own thread. It can be tightened or released by torquing the head. A nut is not required. [4]
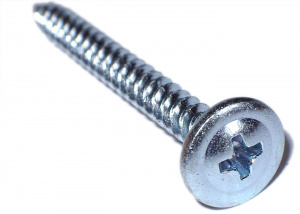
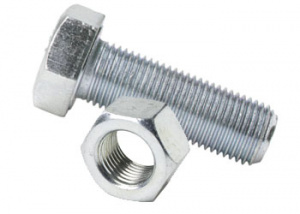
Selection Criteria for Screw Material
- Size
- Required strength
- Resistance to corrosion
- Joint material
- Cost and temperature.
- Mass
Screw Heads
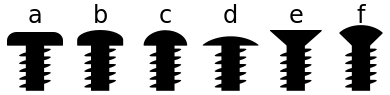
Visit https://en.wikipedia.org/wiki/Screw#Screw_head_shapes for a comprehensive treatment of this topic.
Screw Drives [5]
A screw drive is a pattern which is used to turn a screw. It allows torque to be applied to it usually by using a mating tool, such as a screwdriver, that is used to turn it.
Phillips drive
Phillips drives are among the most common type of screw drives.
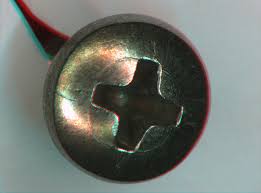
Slotted Drive
The slotted drive, though the oldest drive, is still commonly used today. They are subject to slippage and provide lesser torques than other drives.
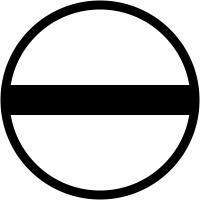
Socket Drive
These drives have a hex shaped internal socket. A hex key or allen wrench is used to tighten or loosen it.
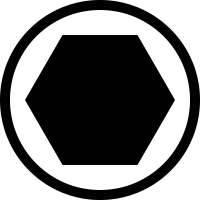
Hex Drive
This one is interesting. It is one of the few drives which is turned the outside of the head rather than the inside. Hex head screws are installed with a socket, usually connected to a ratcheting tool or a power driver.
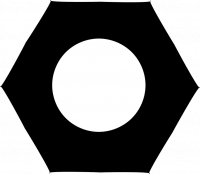
Robertson Drive
These have a square shaped socket which tapers slightly with depth into the screw head. Strong torque is provided by the four 90° angles. They decrease the possibility of slippage.
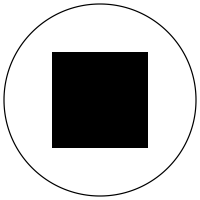
U Drive
Also known as a hammer drive screw, it is set in a properly sized pilot hole. It is then driven into place with a hammer. Quite interestingly, the threads of this screw turn as it is driven, thereby creating the fastening action.
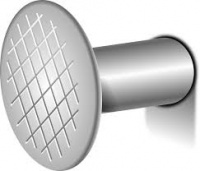
Other types of screw drives are shown in the image below:
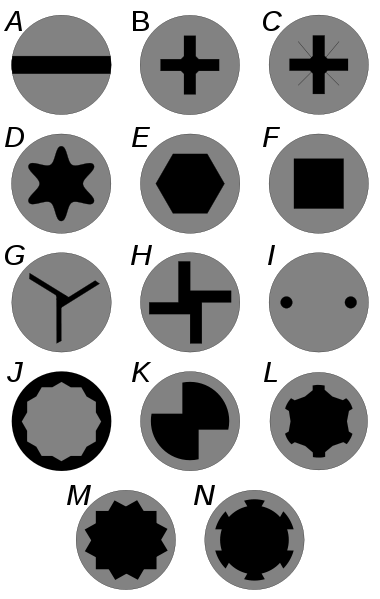
Selection criteria of the screw for satellite
Screws are used to attach any two surfaces in contact on our satellite. The size of the screw will be decided by the maximum depth of penetration of the hole. The screws are generally made of the material SS304 (stainless steel).
Single slotted and Phillips screws tend to slip off while using a screwdriver to screw them.These fasteners are easily damaged at the slot. In addition, these are hard to use with a torque wrench.
Allen/hex head fasteners are very common in most equipment. These are more durable and less likely to slip. This also allows use of torque wrenches. Hence, allen headed screws are a good alternatives.
How tight should a screw be?[6]
The tighter the screw, the more friction there is to resist loosening.
Screws are quite likely to come loose if relative motion takes place between the threads. Static friction is very much higher than sliding friction, so once movement in a direction is onset, it becomes much easier for unscrewing motion to happen.
Bolts are less resistant to shear loads, so higher clamping force and friction should be used to reduce these loads.
Additional tightening preload does not buy any additional fatigue protection as long as joint separation does not happen.
How to achieve the required tightness?
According to the Machinery's handbook, tightening by feel is only +-35% accurate. Using a torque wrench improves the accuracy to only about +-25%. These uncertainties are huge, and thus, we should not to tighten too close to yield, or too loose. They give a good reason to design a joint so that it will still work with a wide range of possible pre-loads. There's a method called "turn-of-nut" which can supposedly get within +-10% accuracy, but it relies heavily on a reliable starting point from which to start counting turns. (see Machinery's handbook).
Additional Information
SAE J429 defines the bolt grades for inch-system sized bolts and screws. It defines them by grade, which ranges from 0 to 8, with 8 being the strongest. Higher grades do not exist within the specification. SAE grades 5 and 8 are the most common.
Metric ISO Marking
Metric fasteners are marked with two numbers separated by a decimal point, like 10.9. The 10 is 1/100th of tensile strength in MPa, and the .9 represents the ratio of yield to tensile strength. So 10.9 represents a tensile strength of 1000 MPa and yield of 900 MPa.
See https://www.boltdepot.com/fastener-information/materials-and-grades/bolt-grade-chart.aspx for more information on these marking schemes.
If you are done reading this page, you can go back to Mechanical Subsystem
References
- ↑ https://en.oxforddictionaries.com/definition/screw
- ↑ https://books.google.co.in/books?isbn=1317938100
- ↑ http://www.solidswiki.com/index.php?title=Screws&mobileaction=toggle_view_mobile
- ↑ http://www.threadall.com/bolts
- ↑ http://www.fastenersuperstore.com/fastener-guides/screws-drive-styles
- ↑ https://www.elexp.com/Images/AllAboutScrews.pdf